
SmoothFlow® Batch Tunnel Washer 150 lb. and 220 lb. Models
Jump To:
Choose a Section
Jump To:
SmoothFlow® Batch Tunnel Washer 150 lb. and 220 lb. Models
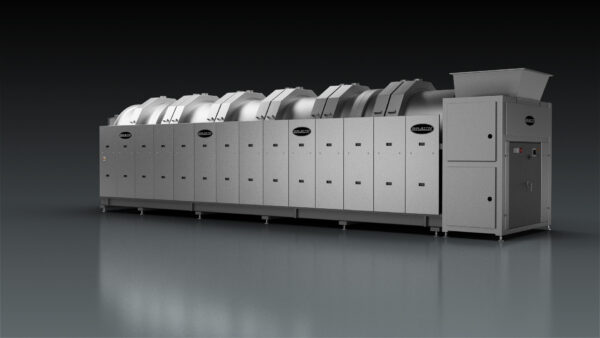
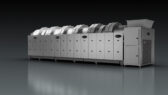
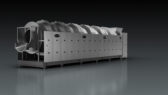
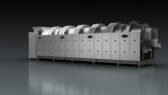
SEE MORE
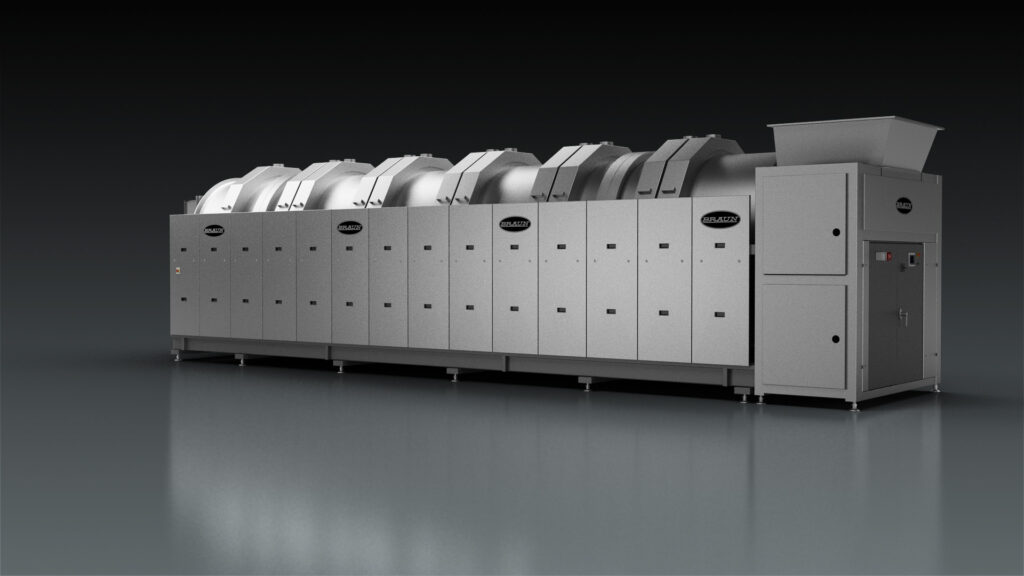
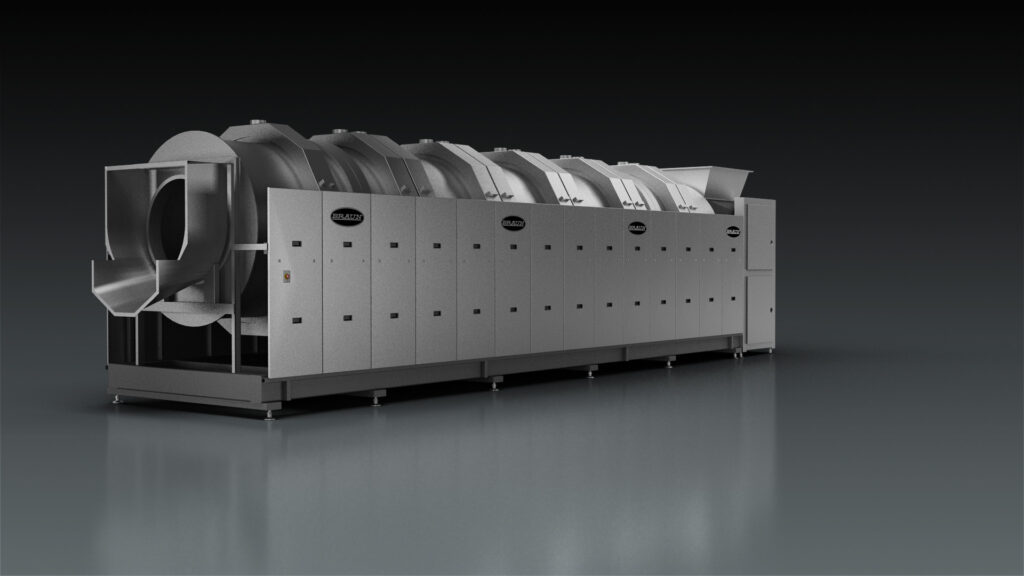
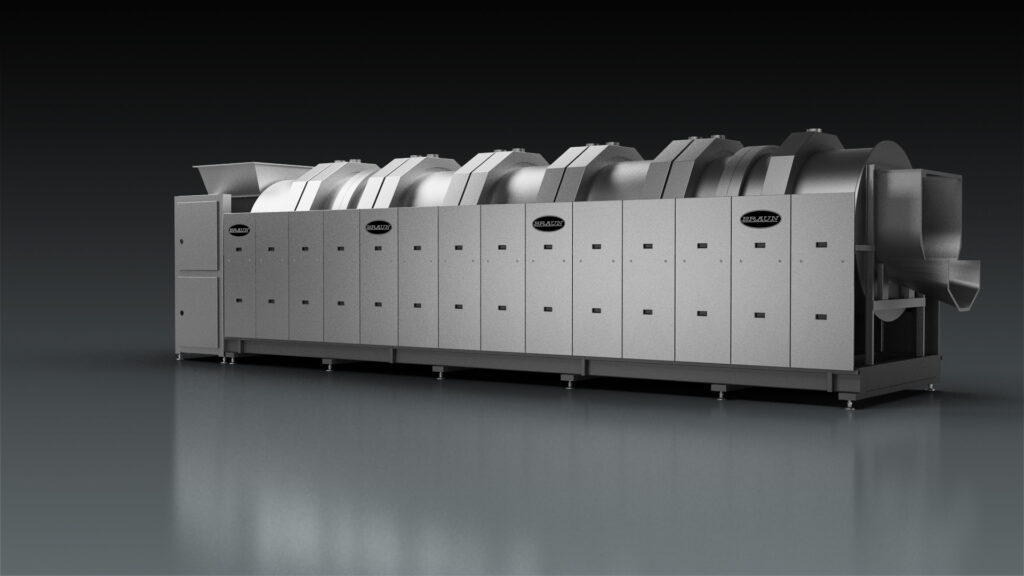
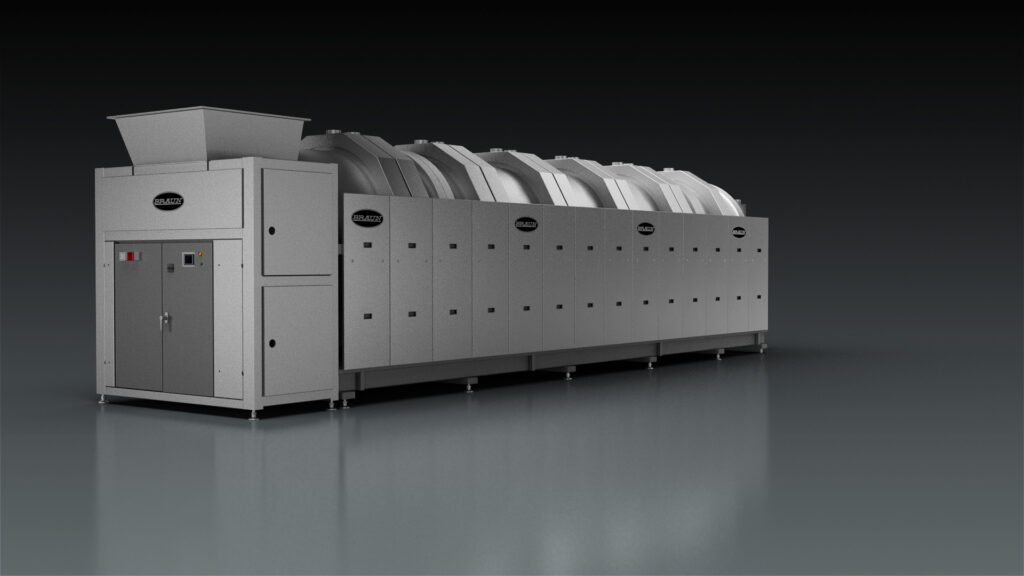
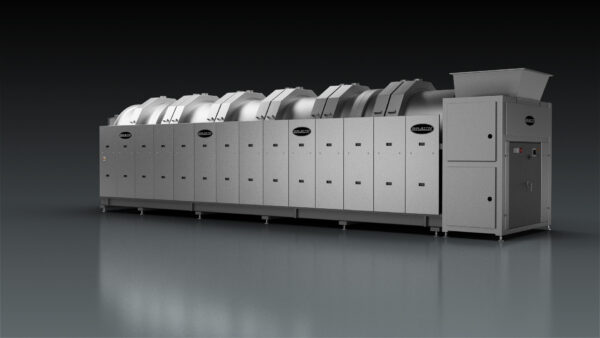
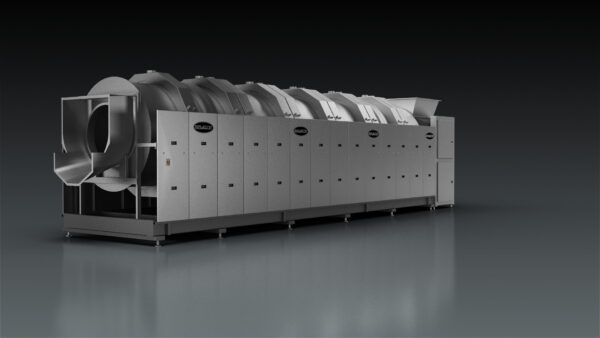
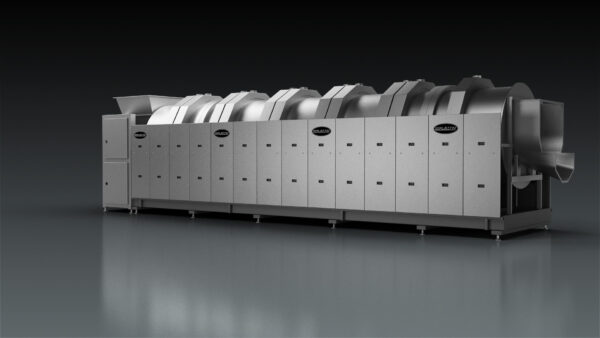
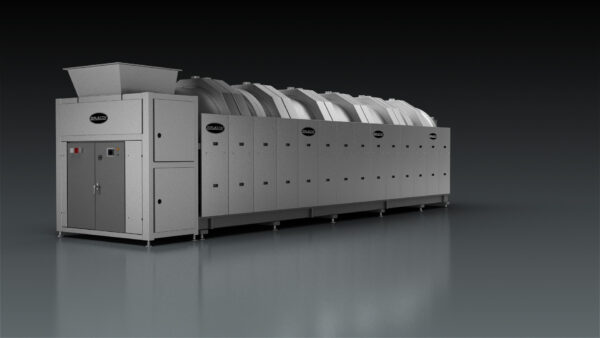
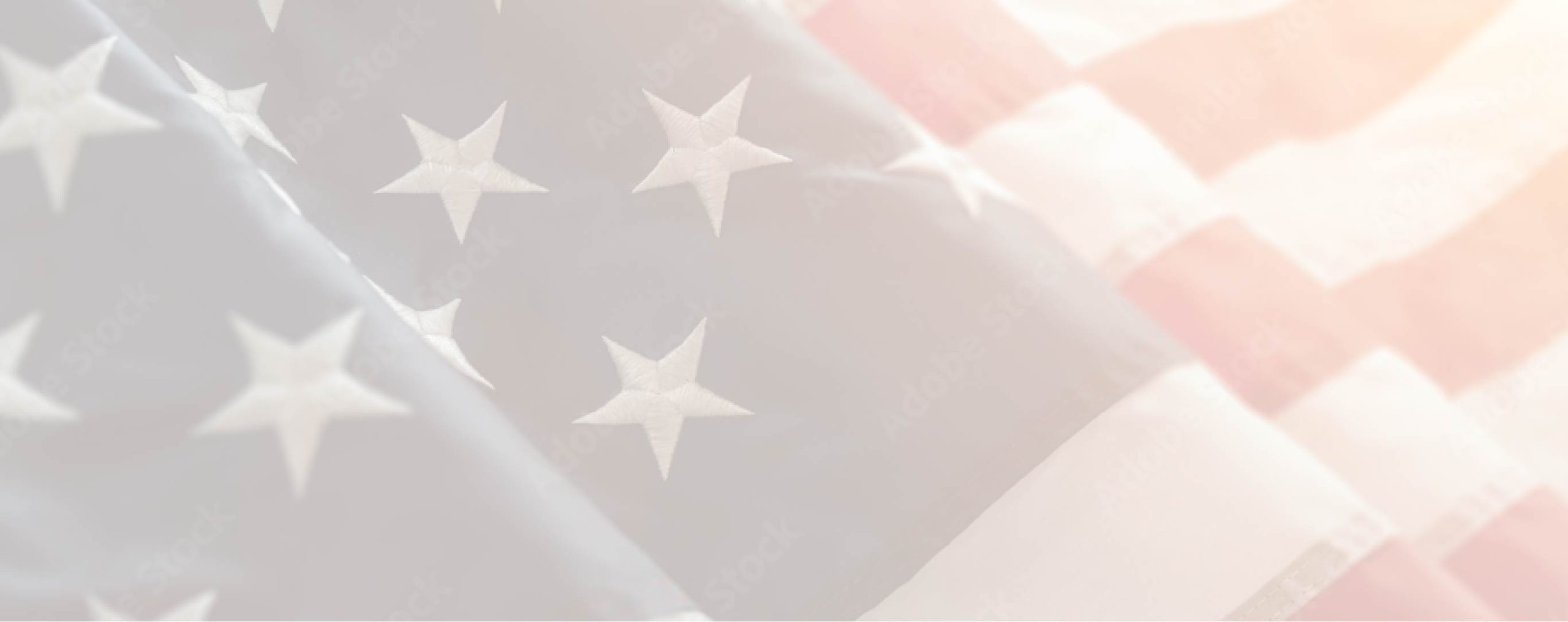
Special Features
Proven Technology
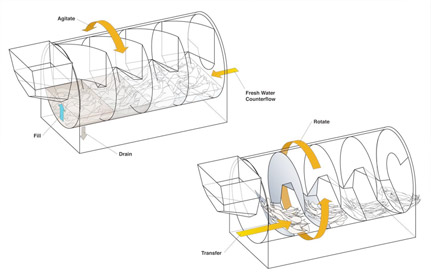
Proven Technology
- Braun’s Tunnel Infusion Technology is used throughout the tunnel. This is Braun’s trademarked fill process of adding water and chemistry above the goods providing superior agitation and mixing.
- Braun’s mono-shell design utilizing stainless steel provides perpetual cleaning of the cylinder affording a processing environment for the effective and hygienic processing of linens.
- Positive transfer process allows for maximum utilization of the machine’s processing capacity.
- Braun tunnels operate with the mechanics of an open helicoid process unlike tunnels using a true archimedial screw.
- Unparalleled mechanical action – each chamber washes with a similar level of mechanical action as an open pocket washer for exceptional wash quality.
- Reverse rotation capability! In the event of a double batch error, Braun tunnels have the ability to reverse rotate manually if needed, eliminating the need to enter the tunnel to clear the goods.
- Between zones, solid compartment walls keep all wash solutions separated
- In the normal standby and transfer positions, total separations exists between batches and 100% batch integrity is assured.
- Counterflow is accomplished through compartment walls, which eliminates inside seals that are difficult to monitor and service.
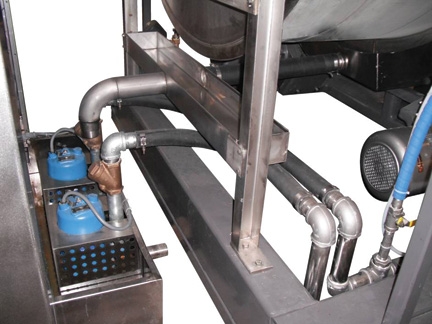
Water Recovery and Reuse
- Exceptional reuse of water provides low water consumption per lb. processed without the risk of total dissolved solid (TDS) build up like other machines in the industry
- Extremely low rewash rates….2% or less – improves linen life
- Hydraulic cooling water from the press….press water is re-used as either rinse, make up water to the wash, or in the pre-wash of the machine
- Recovery of water from seal wettting and unintended overflow to the rinse reclaim tanks
- Every stream in the Braun tunnel is reused at least once
- Water usage on Braun tunnels range from 0.4 – 0.7 gallons per pound of linen depending on the goods soil classification and wash process.

Auto Flow Valve Splitter
The auto flow valve splitter enhances water reuse on Braun tunnels by transferring press reclaim water to the rinse zone. This significantly lowers fresh water use.
Process Flow Diagram (8 Chamber)
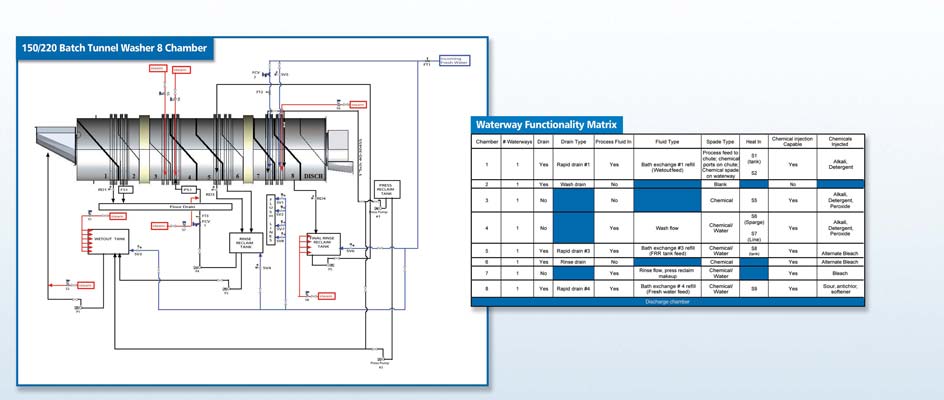
Process Flow Diagram (11 Chamber)
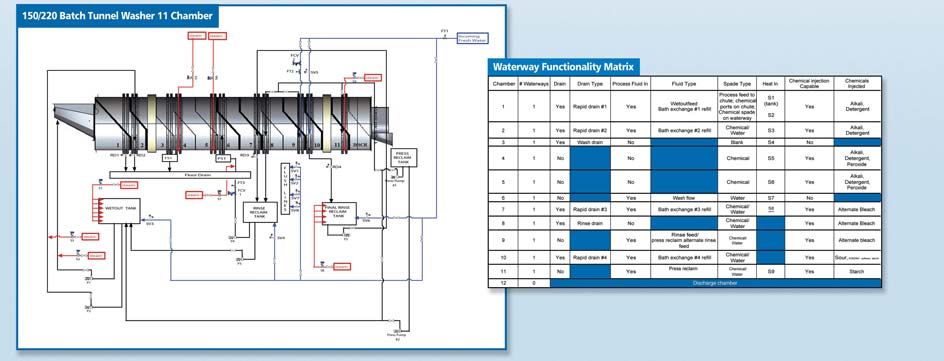
Process Flow Diagram (14 Chamber)
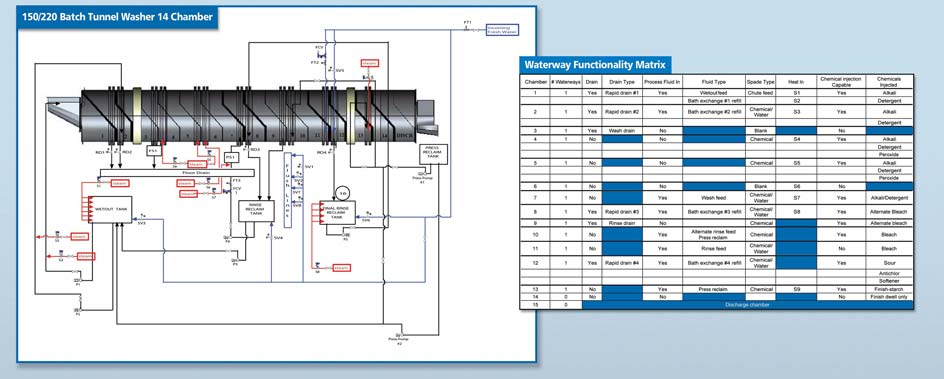
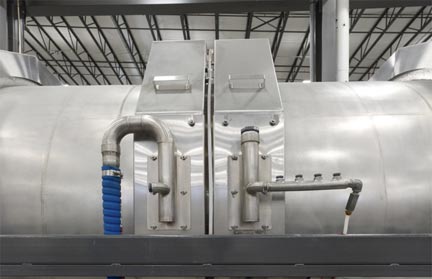
Chemical and Water Injection Area
Water and chemistry are injected at this location with the chemistry added above the water level for proper and thorough mixing.
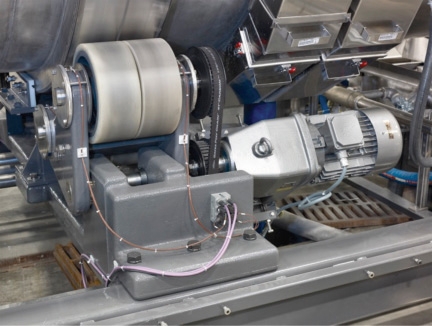
Drive System
- Simple, rugged and reliable – – no chains that may wear or break
- Four drive motors are mounted on ductile iron castings and are easily accessible, providing for an error-free friction drive system with the ability to run on less than four motors if there is maintenance need.
- Braun tunnels monitor bearing operating temperature through the PLC
Heating Systems Overview
The heating system on the Braun BTW is designed for the application of steam to the machine in three different ways. Each of the heat applications on the machine are designed for the highest energy efficiency conversion, as well as for the quickest ramp up to operating temperature.
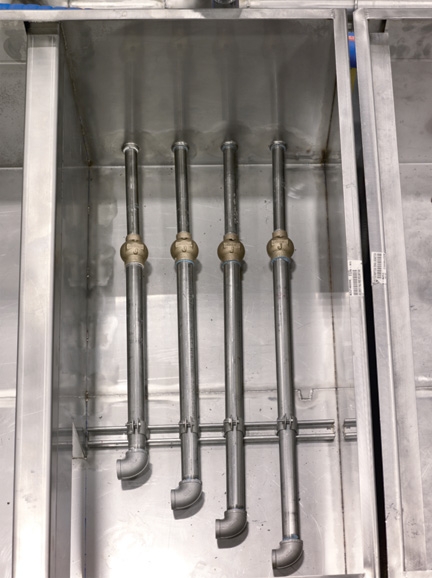
In-Tank Heating (Steam Injectors)
- Utilized for heating reclaimed water in the wetout tank and final rinse reclaim tank
- Heating system sized to meet all industry demands
- Energy efficient direct steam tank injection
- Temperature probe in tanks for indication feedback
- Precision temperature control
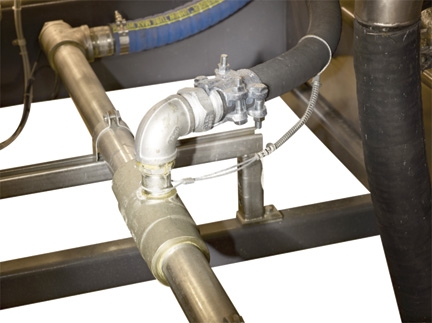
In-Line Heating (Steam Ring)
- Utilized for heating all prewash compartments and main wash flow, can be used for supplemental or primary heating of prewash compartments
- Primary heating for main wash flow
- Energy efficient direct steam line injection in process line while fluid is being transferred
- Temperature probe in pipelines for indication feedback
- Precision temperature control
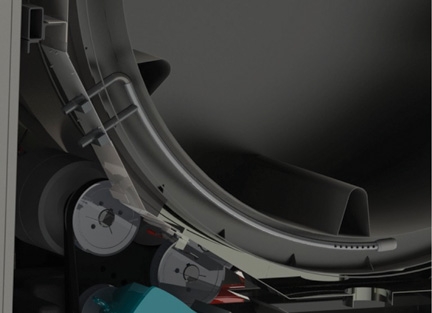
In-Shell Heating
- Sparge Tube (patent pending technology)
- Utilized for heating all necessary wash compartments
- Energy efficient direct steam injection in BTW cylinder to get direct delivery of heat to process
- Temperature probe in shell for indication feedback
- Precision temperature control
- Provides heating capability in one finish compartment for improved extraction and/or starch applications

Main Wash Flow
The wash flow system has both an inductive flow sensor and precision flow control valve to control the flow to the wash zone
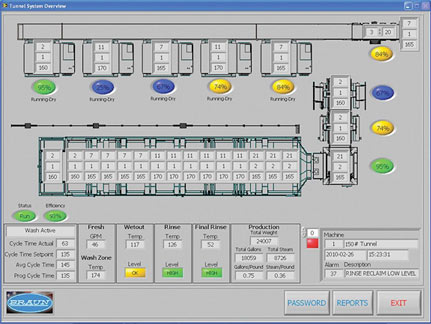
WASHNET® Data Management Software
- An exceptionally powerful tool designed to allow operations managers to optimize site performance through the use of real time data!
- Provides plant operators real time data for making timely decisions proactively.
- Allows Braun technicians the ability to remotely support the technical needs of the operator.
- Allows management to remotely access real-time performance information from any PC.
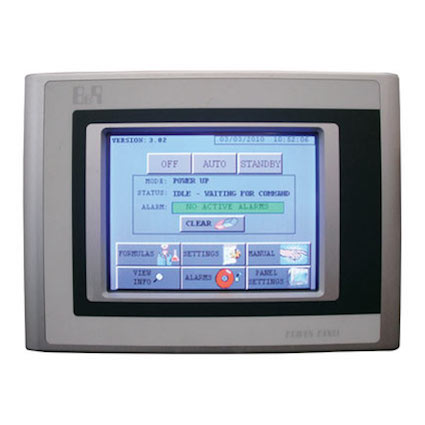
Touch Screen Controls
- Simple, intuitive, and easy to use
- Braun controls aid in formula management and allow for valuable operating data to be available at the touch of a finger.
- Conveniently located usb flash drive to simplify program loading and backup
- 24 Volt Arc Flash Safe Control Panel
- Interchangeable Flash Card/Configurable to Machine
- Operators can pre-program and time every cycle and water temperature and level to an exacting degree.
- Used on all Braun machines
Product Videos
Positive Transfer Process
150 and 220 lb. Tunnel Processing Functionality
Batch Tunnel Washing and Infection Control
Sistema De Tunel De Lavado Desde 150 Hasta 220 Lbs.
Tunnel Process Flow (8 Chamber)
Tunnel Process Flow (11 Chamber)
Tunnel Process Flow (14 Chamber)
Product Literature
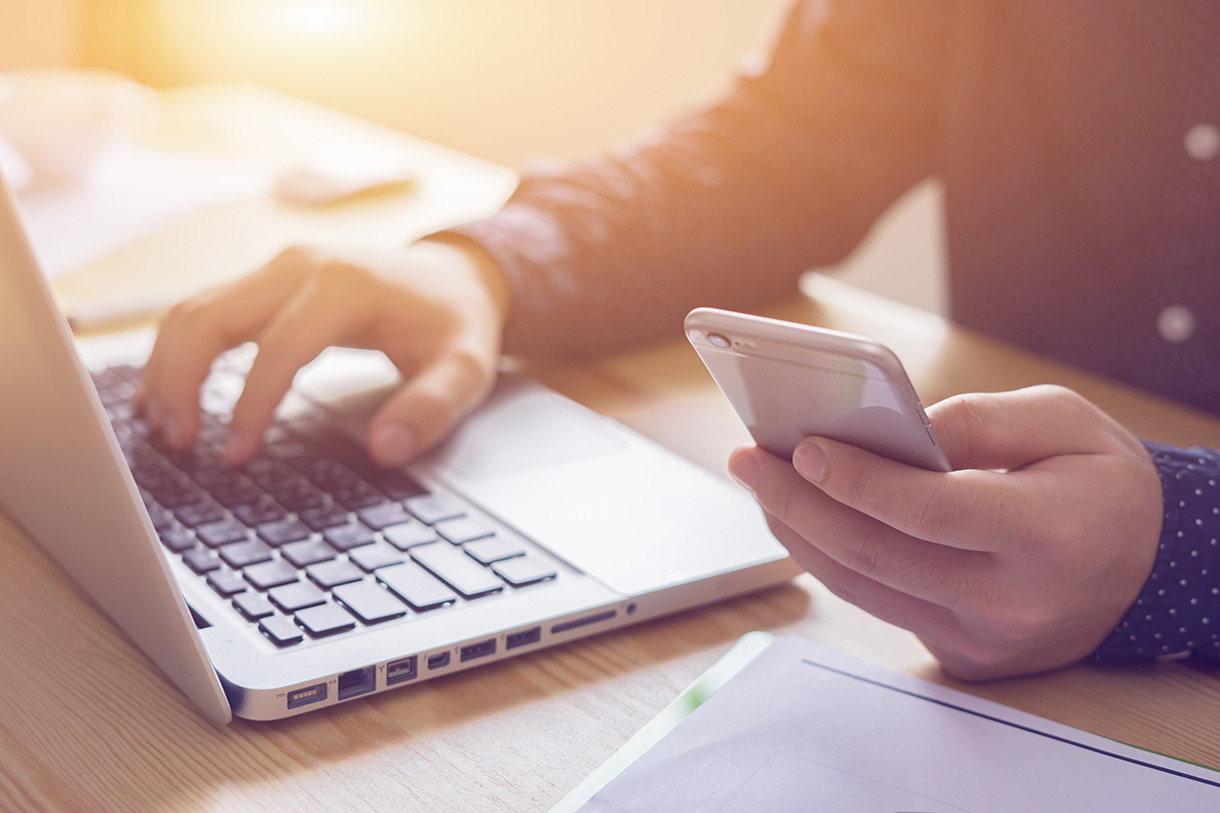